Do-it-Yourself 5 min Lesezeit
Schotteinbau
Wie die Trennwände unter Deck montiert werden
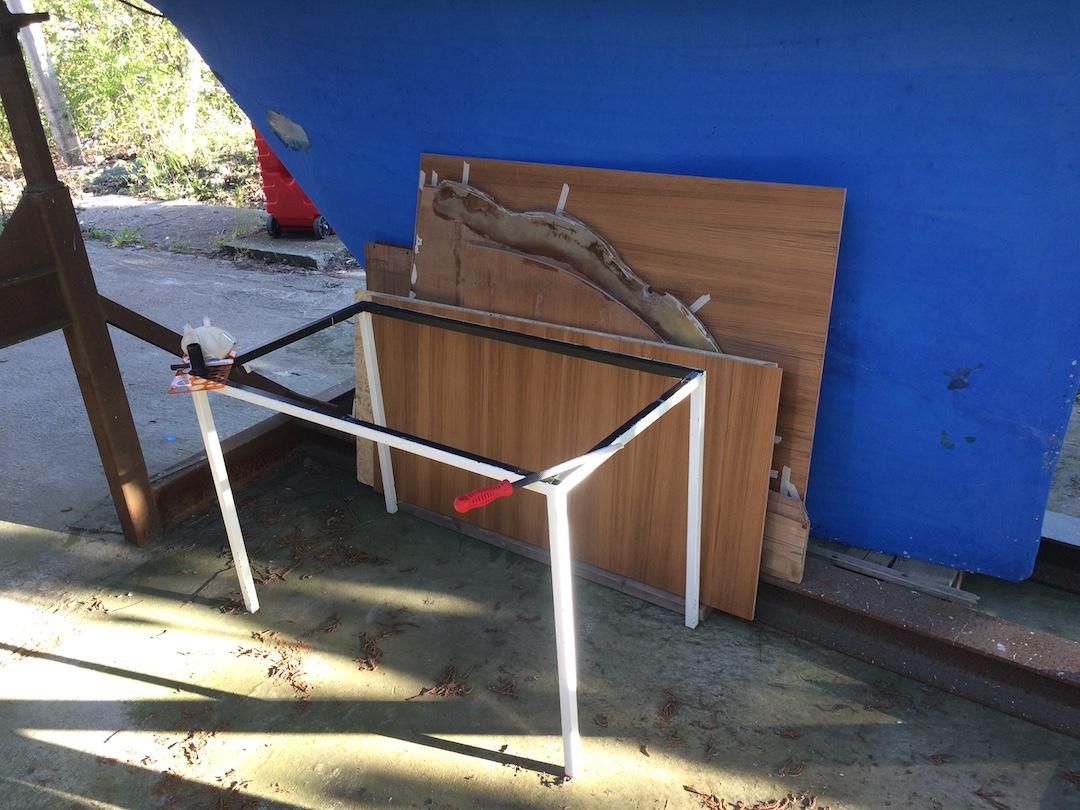
Obwohl die ausgeschnittenen Laminatwinkel beim Ausbau des alten Interieurs bis zur Bordwand entfernt sind, wird die Bordwand mit dem Exzenterschleifer an den Flächen, wo laminiert wird, nochmals angeschliffen. Der Schliff mit grober 24er bis 40er-Körnung gewährleistet eine gute Verbindung der Bordwand mit dem neuen Laminat. Mit einem Exzenterschleifer ist das in wenigen Minuten gemacht. Mit vernünftiger Absaugung geht es sogar halbwegs sauber über die Bühne. Danach wird das Vorschiff gestaubsaugt und mit einem feuchten Lappen gründlich ausgewischt. Glasfaserstaub ist ungesund.
Von Erdmann Braschos, veröffentlicht am 11.10.2024
Das erwartet Sie in diesem Artikel
- letzte Arbeiten an Bord vor der Montage des neuen Interieurs
- Anpassen der neuen Trennwände zwischen den Kajüten
- Vorbereitung eines haltbaren Laminats
- welche Jobs wie viel Arbeit machen
- welche Produkte verwendet wurden
Artikel vorlesen lassen
Hölzer zuschneiden
Das neue Interieur wurde anhand der alten Bretter so weit wie möglich zugeschnitten und mit Umleimern versehen fast fertig an Bord mitgebracht. Bootsbauer Johannes Schultze hat das alles prima vorbereitet. Das beschleunigt den Zusammenbau des Bootes sehr. Auch die obere Kontur unter dem Kajütaufbau und das seitliche Laufdeck ist auf der Trennwand zwischen Bad und Vorschiff fertig zugeschnitten. Nur die Rundung der Bordwand muss anhand des alten Schotts wiederhergestellt werden.
Da es sich beim Ausbau im Herbst mit dem Trennschleifer nur mit groben Schnitten um die Längsversteifungen (Stringer) herum aus dem Rumpf schneiden ließ, stelle ich die Kontur am alten Schott mit angehefteten Pappstreifen bis auf einen halben Zentimeter genau her. Diese Toleranz lässt sich mit der Hohlkehle aus Epoxidharz ausgleichen, das mit Quarzmehl vom Typ West System 406 zu einer zähen, nicht verlaufenden Masse in die Harz-Härtermischung eingerührt wird. Nach dem Anrühren des Harzes wird so viel vom weißen Mehl zugegeben, bis man passend zur Temperatur die gewünschte Konsistenz hat.
Das ist perfekt für steile und sogar überhängende Verbindungen. Der «Kitt» bleibt am Platz. Die etwa daumenbreite Hohlkehle schafft eine gute Grundlage für das Anbringen der Glasfasergelege. Der Radius vermeidet nachteilige Knicke im Laminat zwischen Bordwand und Schott. Wichtig ist, dass nach dem Anbringen der Hohlkehle bald laminiert, spricht nass in nass gearbeitet wird. Das spart einen zusätzlichen Schliff in schlecht zugänglichen Bereichen und die Hohlkehle verbindet sich gleich mit dem Laminat.
Die Kontur der Bordwand mit den Stringern war nach einer halben Stunde abgenommen. Der Zuschnitt mit der Stichsäge dauerte eine ¾ Stunde. Die neue Schottwand wurde in beengten Verhältnissen zwischen Rumpf, Kajütdach und dem seitlichen Laufdeck an seinen künftigen Platz geklappt. Deshalb musste ich weitere Einbauten, die das Einbringen des Schotts behindern, vor der abschließenden Montage ausbauen.
Für das Ausrichten nehmen Segelfreund Uli und ich uns Zeit, damit das neue Schott wie früher zwischen den weiteren, ebenfalls neuen Einbauten fugenlos sitzt. Voraussetzung dazu ist, dass der ursprüngliche Ausbau mit Teaksperrholzplatten in den gleichen 12 und 15 mm Wandstärken erfolgt. Nur so lassen sich die alten Maße übernehmen. Zeitraubende Nacharbeit entfällt.
Ankerkastenschott
Das Ankerkastenschott musste mit derart groben Schnitten per Stichsäge und Winkelschleifer aus dem Bug geholt werden, dass sich Muster und Schablonen kaum eignen. Ich beginne mit einer Pressholzplatte aus dem Baumarkt, ungefähren Maßen anhand der alten Schablone und stelle die Rundung des gewölbten Decks in mehreren Schritten mit einer langen Kiefernleiste auf dem Muster her.
Das Muster nehme ich als Vorlage zum genauen Zuschnitt der Deckswölbung und der Flanken, einschließlich der größeren Ausschnitte für die seitlich auf der Bordwand sitzenden Verstärkungen (trapezförmige Stringer). Hier finde ich einen Kompromiss aus möglichst genauem Sitz und der Aussicht, das Schott überhaupt an Ort und Stelle zu bekommen. Die etwas größeren Spaltmaße lassen sich vor dem Laminieren problemlos mit der beschriebenen Hohlkehle schließen.
Die Maße werden zum Zuschnitt des Schotts auf das neue Brett aus Bootsbausperrholz übernommen. Der Zuschnitt erfolgt auf einem ausrangierten Tischgestell unter dem Boot. Die Anpassung des Musterbretts und des zur Deckswölbung passenden Schotts dauert etwa vier Stunden. Jetzt wird das eigens aus dem Oldtimer-Zubehör besorgte Kederband mit Heftklammern auf den Stirnseiten des Schotts angebracht und das Brett mit einigen Blechschrauben an Ort und Stelle montiert. Natürlich verschwinden die Schraubenköpfe in vorsichtig angebrachten Bohrungen, mit der Japansäge gekürzten und abschließend in Maserrichtung beigeschliffenen Querholzdübeln (Pfropfen).
Mit dem Anbringen der Hohlkehle, Anlaminieren, Beschichten der Vorderseite mit Glasfaser und den aufwendigen, für die Stabilität und Dichtigkeit des Vorschiffs entscheidenden Winkellaminate über fast 4 m Länge beschäftigt sich Ulli einen ziemlich langen Arbeitstag. Anlass für die ganze Arbeit war eine beharrlich gesuchte, über dem alten Ankerkastenschott versteckte Undichtigkeit unter einem unzugänglichen Relingsfuß. Jetzt geht es darum, dass sich der ganze Aufriss mit einem ringsum dichten Laminat auch lohnt. Mehrmals sehen wir uns das Laminat an. Wir tasten es auch in schlecht zugänglichen Winkeln ab, um Luftblasen und etwaige Lecks auszuschließen. Es wird sogar am Tag darauf noch einmal in mehreren Gängen nachgearbeitet.
Nach dem Einbau des vordersten Schotts geht es mit dem Ausbau des Vorschiffs weiter. Der Waschtisch aus Corian, der darunter sitzende Schiebetürrahmen und die aufgemöbelten Ablagen passen und sind in etwa zwei Tagen eingebaut. Es folgt der Schrank mit den Schubladen im Vorschiff, der dank perfekter Vorbereitung durch Johannes Schulze ebenfalls passt wie das Original von anno 1979. Dennoch stecken in den Einbauten mehrere Tage Arbeit.
Die Versuchung ist groß, die unansehnlichen alten Bretter bald wegzuwerfen. Man sollte das auf keinen Fall tun, weil die Vorlage für alte Maße und die Übertragung von Löchern wiederholt gebraucht wird.
Natürlich ist der Vorschiffsausbau damit weiterhin nicht komplett. Im Einbau und Anschluss der Armaturen an die Druckwasserpumpe, Beleuchtung von Waschraum und Vorschiff, Anbringen des Himmels, Montage der Toilette und Schläuche gehen weitere Stunden. Angesichts des Finales geht das alles flott von der Hand.
Laminat
Als Fasermaterial wurde biaxiales, pro Quadratmeter 400 Gramm schweres Glasfasergelege genommen. Je nach Anwendung empfehlen sich hier unterschiedliche Fasern, Zugrichtungen und Faserstärken/Gewichte. Vorgesehen sind vier Lagen aus 10 Zentimeter breiten Gelegen, was ein 1.600 gr/qm Laminat ergibt.
Es werden immer nur kleine Harz-Härter Mischungen angerührt, weil sie sonst warm werden und kochen (die Dämpfe sind ungesund). Praktisch ist, wenn man zu zweit arbeitet, wobei einer das Material (Harz, Pinsel, Gelege) anreicht und einer vor Ort die Flächen zunächst mit der fertigen Epoxidharzmischung einstreicht und dann die Glasfaserstreifen anbringt, zurechtschiebt und sicherstellt, dass alles mit Harz getränkt ist. Der zweite bereitet währenddessen in einem weiteren kleinen Gefäß (Marmeladenglas) die nächste Epoxidharzmischung vor.
Fazit: Der zeitliche Aufwand für die ganze Sache war mit drei vollen Tagen für den Ausbau im Herbst, Planung und Beschaffung der Teile den Winter über und etwa zehn Tagen im Frühjahr groß. Das Ausschneiden der alten Schottwände mit Glasfaserstaub von den abgeflexten Laminatresten war übel. Hinzu kommen die Kosten von knapp 5.000 € für das Material und das vorgefertigte Interieur. Dafür ist das Fußende der Vorschiffskojen jetzt dicht, die Kajüte sieht aus wie neu und als Segelfreund Uli und ich Land sahen, hat es sogar Spaß gemacht.
Alle Produkte wurden vom Autor regulär bezahlt.